Ensuring Signal Integrity: How PLTC Cables Manage EMI and RFI in Industrial Environments
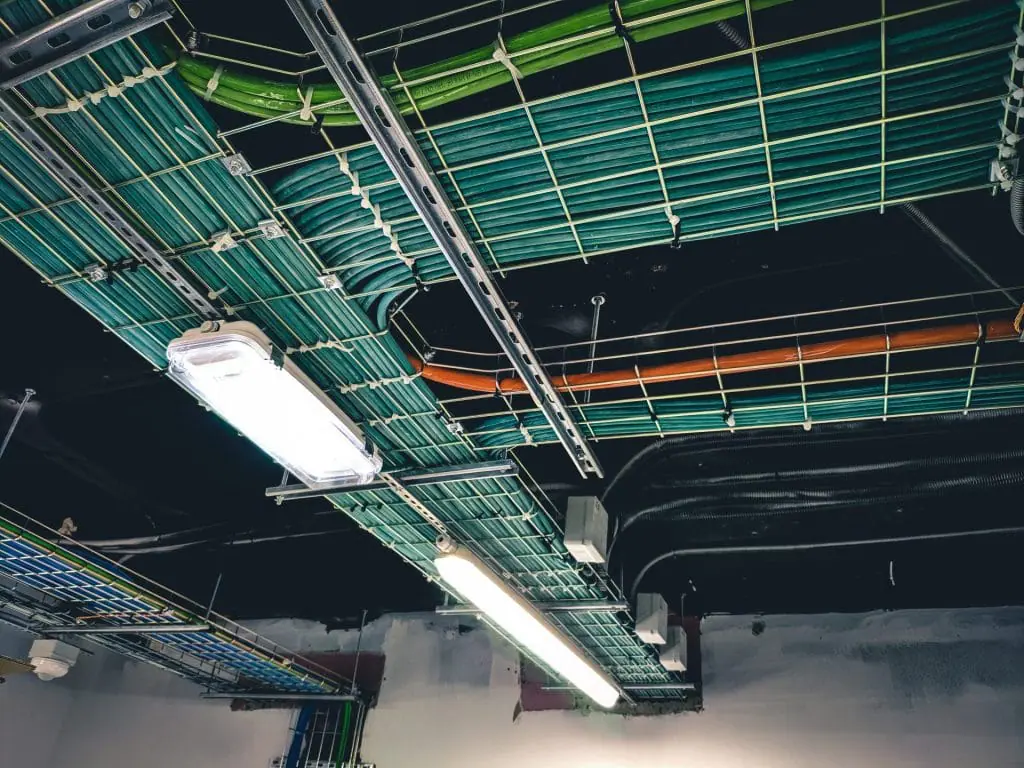
In today’s industrial environments, maintaining clean, reliable signals is crucial for smooth and accurate operation. As manufacturing, automation, and building management systems rely more on digital communications and precise instrumentation, the risk of electromagnetic interference (EMI) and radio frequency interference (RFI) has become a prominent concern. Power-Limited Tray Cables (PLTC CABLES), with their specialized shielding, play a vital role in protecting against these interferences, ensuring signal clarity and operational reliability.
What Are EMI and RFI?
Electromagnetic Interference (EMI) and Radio Frequency Interference (RFI) are electrical noise caused by electromagnetic fields and radio signals. EMI often arises from sources like motors, transformers, and power lines, whereas RFI typically originates from wireless devices. Consequently, in high-power, data-intensive industrial settings, the combined risk of EMI and RFI interference is especially high.
Interference can cause data loss, signal degradation, or erratic system behavior. According to a study by EMC Magazine, data disruptions due to EMI cause nearly 30% of unplanned downtimes in automated facilities. For facilities using automation and IoT, this downtime can lead to substantial financial losses, estimated to cost over $50 billion per year globally across industries.
How PLTC Cables Combat EMI and RFI
PLTC cables are specifically designed for low-voltage power-limited circuits, which makes them ideal for instrumentation and control applications. In these settings, where interference can easily compromise signal integrity, PLTC provide the necessary shielding and reliability. Here’s how PLTC cables manage EMI and RFI:
-
Shielding Materials and Designs
- Foil Shields: Many PLTC cables use aluminum or copper foil shields to create a conductive barrier around the cable’s core, effectively blocking external electromagnetic fields. Foil shielding is commonly used for its lightweight properties and effectiveness in protecting against RFI, which is crucial given that 90% of interference in industrial settings occurs at high frequencies.
- Braid Shields: Braided copper or aluminum shields offer excellent protection against low-frequency EMI. This type of shield is effective for areas near heavy machinery, where low-frequency noise can significantly impact sensitive electronics.
- Combination Shields: Some PLTC cables incorporate both foil and braided shielding, providing up to 98% effectiveness in EMI reduction across a range of frequencies. This combination shielding ensures the highest level of signal integrity, which is critical for data accuracy in process control.
-
Twisted Pair Design
- PLTC often use twisted pairs within the cable core. Twisted pairs can reduce interference by up to 60% due to the way they cancel out electromagnetic noise. This design helps keep signals clear, especially in high-data applications where clarity is essential.
-
Grounding Practices
- Proper grounding of PLTC cables is essential to ensure the shield’s effectiveness. According to the Institute of Electrical and Electronics Engineers (IEEE), proper grounding and shielding practices can reduce interference-related failures by up to 50%. Connecting the shield to ground creates a low-resistance path, allowing unwanted electromagnetic energy to safely dissipate.
-
Durable Jacketing
- PLTC cables come with durable outer jackets resistant to abrasions, chemicals, and extreme temperatures. This added protection helps ensure the integrity of the shield and conductor, withstanding challenging industrial environments and extending the cable’s lifespan by 20–30% compared to non-shielded cables.
Advantages of PLTC in Industrial Settings
PLTC cables’ shielding and robust construction make them ideal for various industrial applications, ensuring signal reliability, safety, and cost-effectiveness.
- Signal Reliability in Complex Systems
- According to the Control Engineering Journal, industrial facilities can see a 40% improvement in signal reliability by using shielded cables like PLTC in environments prone to interference.
- Cost-Effectiveness
- By preventing interference-related disruptions, PLTC cables reduce downtime and maintenance costs, which can account for up to $260,000 per hour in large manufacturing settings. Fewer disruptions translate to higher productivity and significant cost savings, making PLTC a smart choice for facilities looking to boost operational efficiency.
Application Scenarios: Where PLTC Cables Excel
- Automation and Control Systems
- In manufacturing, PLTC cables connect programmable logic controllers (PLCs) to sensors, actuators, and control devices. The cables’ shielding ensures that noise from large motors, conveyors, or heavy machinery does not disrupt control signals, enhancing accuracy and efficiency by up to 30% in automated systems.
- Building Management Systems (BMS)
- In HVAC, lighting, and security systems, PLTC provide stable, interference-free connections, supporting energy savings and optimized climate control.
- Oil, Gas, and Chemical Plants
- In hazardous settings, reliable communication is vital for safety. PLTC cables ensure stable data transfer between control rooms and equipment located in high-interference zones, meeting both OSHA and NEC safety standards.
Best Practices for Installing PLTC Cables to Maximize Shielding
To fully benefit from PLTC shielding, follow these installation practices:
- Maintain Physical Separation: When running PLTC cables alongside power cables, a minimum separation distance of 12 inches helps reduce the risk of interference from high-power sources.
- Use Proper Grounding: Connect the cable shield to ground at one end to create an effective path for collected interference.
- Minimize Bends and Twists: Excessive bending can compromise the shielding’s integrity, reducing its interference-blocking capabilities by up to 15–20%.
Using PLTC cables ensures greater signal clarity and data reliability, essential for safe and efficient operations in complex settings. Statistics show PLTC shielding effectively blocks EMI/RFI, making these cables a valuable investment for productivity and safety in modern industry.
Further Reading and Resources
For more information, consult these resources:
- National Electrical Code (NEC): Detailed standards for power-limited tray cables and other low-voltage installations.
- IEEE Standards for Instrumentation and Control: Guidelines for shielding and grounding practices in industrial environments.
- UL Standards for PLTC Cables: Compliance and safety requirements for PLTC across industrial applications.
View BWC’s Power-Limited Tray Cable Products