Aluminum Wiring vs Copper: Pros, Cons, and Applications
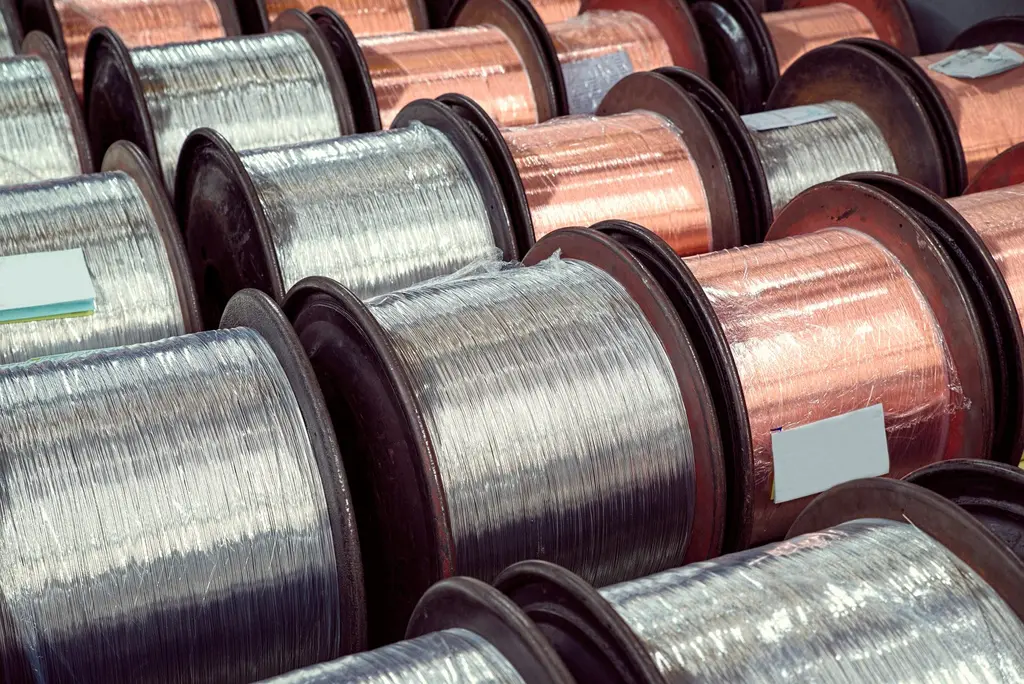
Wiring is a fundamental component of any electrical system, and the choice between copper and aluminum is an important decision in both residential and industrial applications. Each material has distinct properties that affect cost, performance, safety, and longevity. This article explores the differences between copper and aluminum wiring, comparing their advantages, disadvantages, and common applications to help you make an informed choice.
1. Electrical Conductivity and Performance
Copper:
- Copper is an excellent conductor of electricity, offering a higher electrical conductivity than aluminum.
- It has a conductivity rating of 100% IACS (International Annealed Copper Standard), meaning it allows electrical current to flow with minimal resistance.
- Copper wiring is more resistant to heat and electrical load fluctuations, reducing the risk of voltage drops.
Aluminum:
- Aluminum has a lower conductivity than copper, around 61% IACS, meaning it requires a larger diameter wire to carry the same current as copper.
- It is more prone to oxidation, which can lead to resistance build-up and overheating if not properly maintained.
- Although aluminum is lighter, it is more brittle and susceptible to breakage under stress.
2. Cost-Benefit Analysis
Copper:
- Higher upfront cost: Copper is significantly more expensive, with prices fluctuating between $3.50 to $4.50 per pound (as of recent market trends).
- Longer lifespan: Copper wiring has a longer operational life with fewer maintenance requirements.
- Lower energy loss: Due to its superior conductivity, copper experiences lower energy loss, making it more efficient in the long run.
Aluminum:
- Lower material cost: Aluminum is much more affordable, priced around $1.00 to $1.50 per pound, making it an attractive option for large-scale projects.
- Larger wire size needed: Since aluminum is less conductive, larger gauge aluminum wires are required to match copper’s performance, slightly offsetting its cost advantage.
- Higher maintenance: Aluminum wiring requires more frequent inspections due to expansion/contraction issues, which can loosen connections over time.
3. Safety Considerations
Copper:
- Copper wiring is less prone to thermal expansion, meaning it maintains strong and stable connections over time.
- It is less likely to overheat, reducing the risk of electrical fires.
- It is less affected by corrosion and oxidation, maintaining conductivity longer without additional coatings or treatments.
Aluminum:
- Prone to oxidation: Aluminum reacts with oxygen to form aluminum oxide, which increases electrical resistance and generates excess heat.
- Thermal expansion issues: Aluminum expands and contracts more than copper, which can cause connections to loosen over time, leading to potential fire hazards if not properly installed.
- Requires special connectors: To mitigate safety risks, aluminum wiring must be used with rated connectors and anti-oxidant compounds.
4. Common Applications: When and Where Each is Used
Copper Wiring Applications:
- Residential Wiring: Used for indoor outlets, lighting, and appliances due to its reliability and safety.
- High-Risk Environments: Hospitals, data centers, and critical infrastructure where performance and durability are crucial.
- Automotive and Aerospace: Copper’s high conductivity and corrosion resistance make it ideal for vehicle wiring.
- Underground and Outdoor Installations: More resistant to moisture and corrosion.
Aluminum Wiring Applications:
- Utility and Power Distribution: Aluminum is widely used in high-voltage transmission lines due to its light weight and lower cost.
- Large Commercial Buildings: Used for feeder cables and service entrances, where large wire sizes help offset its conductivity limitations.
- Renewable Energy Projects: Wind and solar farms often use aluminum for cost-effective large-scale electrical transmission.
- Temporary Installations: Construction sites and temporary power solutions where cost efficiency outweighs longevity.
5. Conclusion: Which One Should You Choose?
The choice between copper and aluminum wiring depends on the application, budget, and safety requirements.
- For residential wiring and critical systems → Copper is the best option due to its higher conductivity, durability, and safety.
- For large-scale industrial and utility projects → Aluminum is a cost-effective solution when using properly rated and installed components.
- For high-power applications → Aluminum is commonly used in power distribution, while copper is preferred for lower-voltage precision applications.
Both materials have their place in the industry, and choosing the right one depends on the specific demands of your project. If cost is a major factor, aluminum wiring can be a viable choice, but it requires careful installation and maintenance to ensure long-term safety and reliability.
Looking for expert advice on wire and cable selection? Contact us today to find the best solution for your needs!
SHOP BWC PRODUCTS