Behind the Scenes: How Wire is Manufactured from Raw Material to Final Product
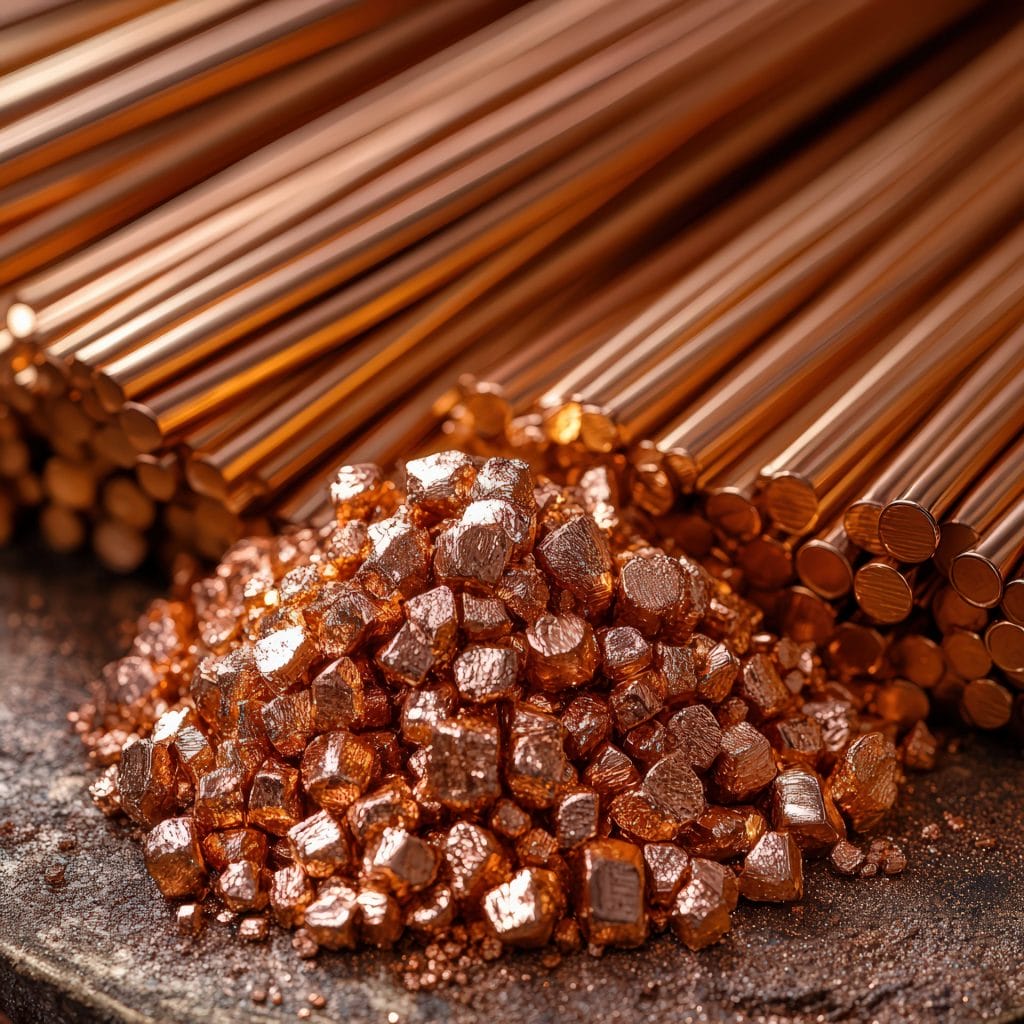
Introduction
Ever wondered how electrical cable powers homes, buildings, and underground systems? The process of wire manufacturing is a fascinating journey that transforms raw materials like copper and aluminum into high-quality cables that power the world. In this blog post, we’ll take you behind the scenes to explore the key steps involved in cable production—from raw material extraction to the final product ready for installation.
Step 1: Raw Material Selection and Extraction
The journey of wire manufacturing begins with selecting high-quality raw materials. The most commonly used metals for electrical wire are:
- Copper – Known for its excellent conductivity and durability.
- Aluminum – A cost-effective and lightweight alternative, often used in power transmission lines.
These metals are extracted from ore deposits through mining and then refined through a process called electrolysis to remove impurities and ensure high electrical conductivity.
Step 2: Wire Rod Production (Casting and Rolling)
Once the raw materials are refined, they are melted down and cast into large rods. These wire rods serve as the base material for wire and cable manufacturing. The rods are then passed through a rolling mill, reducing them to the required diameter while ensuring uniform thickness and high tensile strength.
Step 3: Drawing the Wire to the Desired Size
The wire rods are then cold-drawn through a series of progressively smaller dies to achieve the desired gauge (thickness). This process is crucial as it determines the wire’s flexibility, strength, and conductivity.
- The wire moves through a series of dies, steadily shrinking in diameter while stretching in length. Lubrication reduces friction and prevents breakage, ensuring a smooth process. Depending on the required thickness, the wire may pass through multiple stages.
At this stage, the wire is still bare and needs additional processing to improve its performance and durability.
Step 4: Annealing (Heat Treatment for Flexibility)
To ensure the wire is not too brittle, it undergoes annealing—a heat treatment process that softens the metal, making it more flexible.
- The wire is heated to a high temperature and then slowly cooled.
- This enhances its workability without compromising its electrical properties.
Copper wires, in particular, benefit from annealing, as it restores their ductility after being drawn into thin strands.
Step 5: Stranding (Single Wire vs. Multi-Strand Conductors)
At this stage, manufacturers choose whether to keep the wire as a solid conductor (a single piece of metal) or twist multiple thin strands together to create a stranded conductor.
- Solid Wire – Used for permanent installations, offering lower resistance and higher conductivity.
- Stranded Wire – More flexible and suitable for applications requiring movement, such as automotive and appliance wiring.
Stranding strengthens durability and prevents breakage in applications where wires bend or move frequently.
Step 6: Insulation & Jacketing
To protect the wire from external damage and electrical hazards, it is covered with an insulating material such as:
- PVC (Polyvinyl Chloride) – Commonly used for general electrical wiring.
- XLPE (Cross-Linked Polyethylene) – Provides better heat resistance, often used in high-voltage applications.
- Rubber or Silicone – Used in flexible and high-temperature environments.
The insulation process typically involves:
- Extrusion – The wire is fed through an extrusion machine, where molten plastic is applied.
- Cooling & Hardening – The coated wire passes through a cooling chamber to solidify the insulation.
Some wires may receive an additional outer jacket for extra protection, especially for underground or outdoor use.
Step 7: Quality Testing & Certification of the Wire
Before the cable reaches the market, it undergoes rigorous testing to ensure it meets safety and performance standards.
Common tests include:
- Voltage & Dielectric Strength Testing – Ensures the insulation can withstand high voltages.
- Tensile Strength Testing – Checks the wire’s durability and resistance to breaking.
- Conductor Resistance Testing – Confirms the cable meets electrical conductivity requirements.
Manufacturers follow industry standards such as UL (Underwriters Laboratories), NEC (National Electrical Code), and ISO (International Organization for Standardization) to guarantee product reliability.
Step 8: Cutting, Packaging & Distribution
Once testing is complete, the cable is cut into standard lengths or custom sizes based on customer needs.
- Small spools or coils – Used for retail and small-scale electrical projects.
- Large reels or drums – Supplied for industrial and commercial applications.
Manufacturers ship the final products to distributors, wholesalers, and contractors, who deliver reliable electrical installations worldwide.
Conclusion
Whether it’s powering homes, businesses, or industrial facilities, the cable manufacturing industry plays a crucial role in ensuring reliable electrical connectivity. From the careful selection of raw materials to the precision of the final quality tests, each step in the process is essential for producing durable, high-performance cables. As technology advances, innovations in materials, manufacturing techniques, and sustainability practices continue to shape the future of the industry, ensuring even greater efficiency and reliability. Understanding this journey helps us appreciate the complexity behind the wires we often take for granted.
View our Wire & Cable Products