Taking Flight with Specialized Aerospace Cables
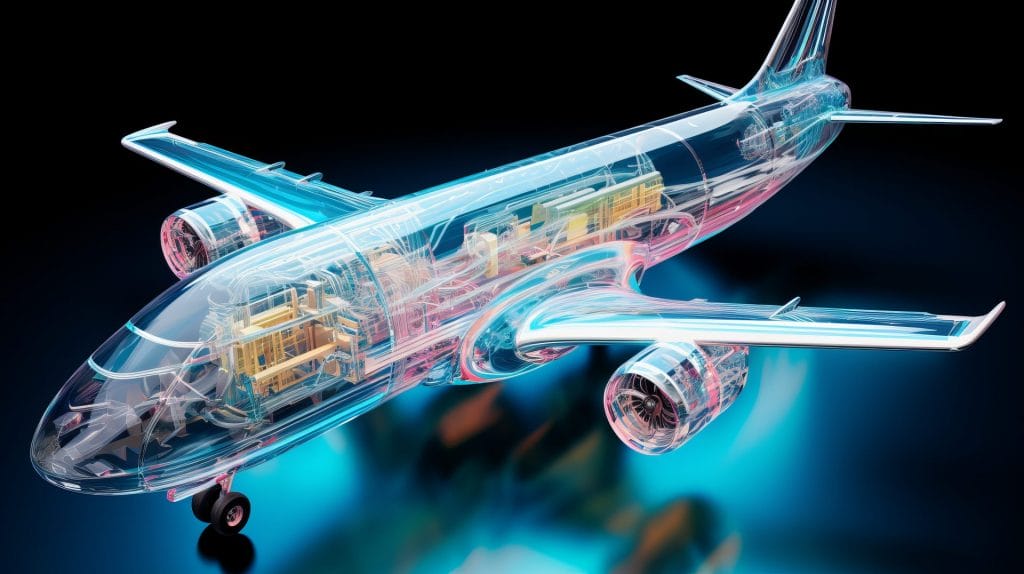
The aerospace industry relies on highly specialized cables to ensure the safe and reliable operation of aircraft, spacecraft, and defense systems. These cables are engineered to withstand extreme conditions, including high temperatures, pressure, vibration, and exposure to chemicals and radiation. Aerospace cables are essential for various applications, such as power distribution, data transmission, and communication within these complex systems.
Why Specialized Cables?
Why Specialized Cables?
The demanding environment of aerospace applications necessitates cables with unique properties:
High-Temperature Resistance
From the frigid temperatures at high altitudes to the intense heat generated by engines, aerospace cables must operate reliably across a wide temperature range. Materials like Teflon and PTFE are often used for their ability to resist high temperatures without degrading.
Durability and Flexibility
Cables in aerospace settings need to withstand constant vibration, mechanical stress, and exposure to harsh environmental conditions. Flexibility is equally important, as cables must be routed through tight spaces within aircraft and spacecraft.
Lightweight Design
Weight is a critical factor in aerospace design. Lighter cables contribute to fuel efficiency and overall aircraft performance. Aluminum wires and fiber optic cables are frequently used for their lightweight properties without compromising performance.
Fire Resistance
Safety is paramount in aerospace applications. Cables must be fire-resistant to prevent electrical faults and fires that could jeopardize the aircraft and its occupants. Specialized coatings and materials are often applied to meet fire safety standards.
Signal Integrity
Reliable signal transmission is crucial for critical systems like communication, navigation, and flight control. Shielded cables are commonly used to protect signals from electromagnetic interference (EMI), ensuring seamless operation. Braided cables provide excellent protection against electromagnetic interference (EMI) and radio frequency interference (RFI) . This shielding is vital in aerospace environments where sensitive electronic equipment needs to operate without interference from other devices or external sources. The braiding acts as a barrier, preventing electromagnetic signals from disrupting the cable’s signal integrity.
Types of Aerospace Cables
Types of Aerospace Cables
A wide variety of cable types are employed in aerospace applications, each designed to meet specific requirements:
Data Cables
These cables transmit signals for various data applications, including avionics and in-flight entertainment systems. Common types include fiber channel, Ethernet, USB, and Serial ATA cables.
Power Cables
Power cables transmit electricity to essential systems within aircraft and spacecraft. Copper wires, often tin-plated for added corrosion resistance, are a popular choice.
Coaxial Cables
Used for carrying high-frequency signals, coaxial cables are essential for communication systems, radar, and navigation equipment. Their shielding helps maintain signal integrity by preventing interference.
Fiber Optic Cables
Fiber optic cables use light to transmit data at high speeds, making them ideal for avionics, advanced communication systems, and in-flight entertainment.
Ribbon Cables
Featuring multiple conductors in a flat, ribbon-like configuration, these cables are often used for connecting electronic devices and transmitting data in compact spaces.
Wire Rope
This durable wire is used for mechanical applications, such as controlling flight mechanisms and providing structural support in aircraft, blimps, and weather balloons.
Challenges of Aerospace Cable Design
Challenges of Aerospace Cable Design
Designing cables for aerospace use presents unique challenges:
Extreme Environmental Conditions
Aerospace cables must withstand a wide range of temperatures, pressure changes, and humidity fluctuations. This requires innovative materials and designs to maintain performance.
Vibration and Mechanical Stress
The constant vibration and mechanical stress encountered during flights can lead to wear and tear. High-performance materials and meticulous engineering are essential to ensure longevity.
Weight and Space Constraints
Cables must be both lightweight and compact to meet the strict design requirements of modern aircraft and spacecraft. This necessitates the use of advanced materials and space-saving designs.
Safety and Reliability
Safety is non-negotiable in aerospace applications. Cables must meet rigorous testing and certification standards to ensure they function reliably under all conditions. A failure could have catastrophic consequences, making reliability paramount.
Innovations in Aerospace Cable Technology
Innovations in Aerospace Cable Technology
The aerospace industry continually drives innovation in cable technology. Recent advancements include:
Advanced Materials
New materials, such as high-performance polymers and composites, are being developed to create lighter and more durable cables. These materials also improve resistance to extreme conditions, including radiation in space. Carbon Nanotubes (CNTs) are incredibly strong and lightweight, with excellent electrical and thermal conductivity. They can be used as conductors or in shielding, offering significant weight savings compared to traditional copper.
Miniaturization
Cables are becoming smaller and more efficient, helping to save weight and space while maintaining or improving performance.
Enhanced Manufacturing Processes
Improved manufacturing techniques, such as precision extrusion and advanced shielding methods, result in cables that are more robust and reliable. Braided cables are more flexible than single-strand wires, making them easier to install in the tight spaces common in aircraft and spacecraft. The braided structure also provides greater durability, allowing the cables to withstand vibration and flexing without damage . This is essential in aerospace applications where cables are constantly subjected to movement and stress.
Hybrid Cables
Hybrid cables combine power, data, and signal transmission into a single unit, reducing weight and simplifying installation while increasing efficiency.
Industry Statistics
Industry Statistics
- The global aerospace cable market is projected to grow from $1.2 billion in 2021 to $1.8 billion by 2026, at a compound annual growth rate (CAGR) of 8.4% (Source: MarketsandMarkets).
- Fiber optic cables account for approximately 40% of the data transmission systems used in modern aircraft, driven by the need for high-speed, low-weight solutions.
- Lightweight materials, such as aluminum wiring, can reduce the overall weight of an aircraft by up to 10%, significantly improving fuel efficiency.
- The average commercial aircraft uses over 150 miles of wiring, highlighting the critical role cables play in aviation systems.
- Aerospace cable failures account for less than 0.1% of all aviation-related malfunctions, thanks to rigorous safety standards and testing protocols.
Resources for Further Reading
- NASA – Standards for Electrical Wire and Cable
- Federal Aviation Administration (FAA) – Aircraft Electrical Wiring
- Institute of Electrical and Electronics Engineers (IEEE) – Aerospace Cable Standards
- European Space Agency (ESA) – Materials for Space Applications
Specialized aerospace cables are vital components that enable the safe and efficient operation of modern aerospace systems. As technology advances, these cables continue to evolve, pushing the boundaries of what is possible in aviation and space exploration.