Beyond Oil Resistance: The Multifunctional Benefits of FEP Cables in Industrial Settings
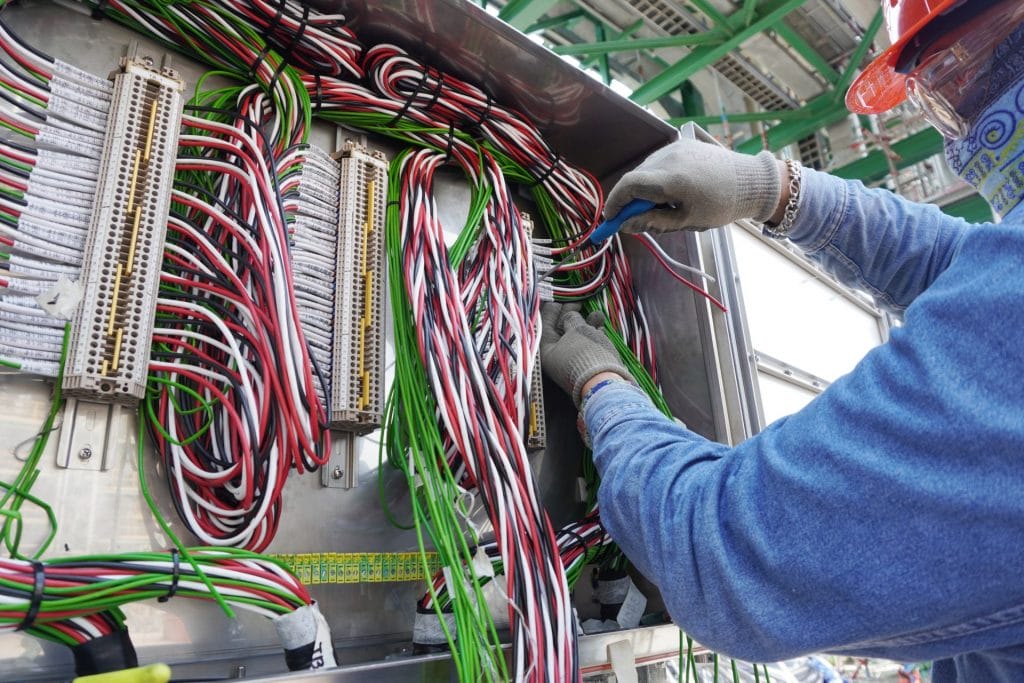
In industrial settings, equipment faces harsh conditions like high temperatures, chemicals, and wear. Fluorinated Ethylene Propylene (FEP) cables excel here, offering oil resistance, durability, chemical resistance, and electrical efficiency, making them an indispensable and versatile choice where standard materials fall short.
This article explores the key attributes of FEP cables and why they are increasingly favored for critical industrial tasks.
Key Aspects of FEP’s Chemical Structure:
- Fluorine-Carbon Bonds: FEP’s backbone consists of carbon atoms with fluorine atoms attached. The carbon-fluorine (C-F) bonds are one of the strongest in organic chemistry, giving FEP exceptional chemical and thermal stability. These bonds are highly resistant to breaking, making FEP extremely resistant to oils, solvents, and many corrosive chemicals.
- Tetrafluoroethylene and Hexafluoropropylene Monomers: FEP is created by copolymerizing tetrafluoroethylene (TFE) with hexafluoropropylene (HFP).Tetrafluoroethylene (TFE) provides a stable backbone, while hexafluoropropylene (HFP) introduces branching that enhances flexibility. As a result, this combination of structural features not only contributes to the unique properties of FEP but also makes it easier to process than other fluoropolymers, such as polytetrafluoroethylene (PTFE). Consequently, manufacturers can utilize FEP in a wider range of applications due to its improved workability and performance characteristics. This balance of stability and flexibility is key for industrial applications.
- Non-Polar Structure: The high electronegativity of fluorine atoms creates a non-polar and non-reactive surface. This helps prevent interactions with oils, fuels, and other hydrocarbons, which makes FEP cables inherently resistant to oil absorption or chemical damage.
- High Melting Point: The carbon-fluorine bonds contribute to FEP’s high melting point, generally around 260°C (500°F). This allows Fluorinated Ethylene Propylene cables to perform in high-temperature environments without melting or deforming, which is essential for industrial applications.
Why FEP Cables Are More Than Just Oil Resistant
1. Exceptional Chemical Resistance
- Chemical Compatibility: FEP’s stable chemical structure resists a wide range of chemicals, including oils, fuels, solvents, and corrosive agents. Unlike standard cables, FEP cables maintain their integrity and performance even with continuous exposure in industrial environments.
- Real-World Applications: Industries such as pharmaceuticals, chemical manufacturing, and refineries often require materials that can withstand daily exposure to caustic substances. FEP’s resistance to degradation from these chemicals helps minimize the risk of breakdowns, making it ideal for applications in such demanding environments.
2. High-Temperature Tolerance
- Temperature Range: FEP cables can function in environments ranging from -200°C to +200°C, and some specialized FEP cables can withstand even higher temperatures. This exceptional range allows FEP cables to perform in high-heat applications that other materials cannot withstand.
- Key Industries Benefiting from Heat Tolerance: Sectors like automotive, aerospace, and industrial processing often operate in high-temperature settings. FEP’s thermal stability prevents it from softening, melting, or releasing harmful substances under heat, making it suitable for use near engines, in high-power electronics, and around machinery that generates intense heat.
3. Electrical Efficiency and Dielectric Properties
- Low Dielectric Constant and Dissipation Factor: FEP is known for its excellent insulation properties, which enable stable, loss-free signal transmission. This low dielectric constant means minimal signal loss and power leakage, making FEP cables suitable for high-frequency and high-voltage applications.
- Applications in Communication and Control: The superior electrical efficiency of FEP cables makes them ideal for applications where precision and data integrity are essential, such as communication systems, control circuits, and industrial automation. Moreover, in these environments, reliable data transmission is paramount. FEP’s excellent electrical properties not only enhance signal quality but also help ensure uninterrupted performance. As a result, FEP cables provide the reliability and efficiency that critical systems demand, making them a preferred choice for modern industrial applications.
4. Environmental Durability and Mechanical Strength
- UV and Weather Resistance: FEP cables can withstand long-term exposure to UV rays, water, and ozone without deteriorating, making them suitable for both indoor and outdoor applications. This makes FEP cables particularly beneficial in industries where equipment is installed in open or partially exposed environments.
- Abrasion and Mechanical Wear Resistance: Beyond chemical and environmental resilience, FEP’s robust physical structure offers high resistance to abrasion, flexing, and general wear, making it durable enough for industrial automation, robotics, and machinery that experiences constant movement.
FEP Cable Use Cases in Industrial Applications
FEP’s versatility and durability make it invaluable across a variety of industries, especially in demanding environments where standard materials would degrade quickly:
- Automotive and Aerospace: FEP cables are used in areas with exposure to oils, fuels, and high temperatures, such as near engines and exhaust systems. The material’s temperature tolerance and oil resistance make it ideal for critical applications where reliability is essential.
- Industrial Manufacturing: In chemical plants and manufacturing facilities, FEP cables power systems exposed to harsh chemicals and abrasive materials, ensuring reliability and reducing the need for frequent replacements.
- Power and Communication Systems: With excellent dielectric properties, FEP cables are ideal for data and power transmission in industrial control systems, providing a stable and interference-free connection.
- Medical and Laboratory Equipment: FEP’s resistance to chemical sterilization agents and high temperatures allows it to function in medical and lab equipment, where sterilization and contamination control are vital.
Choosing the Right FEP Cable for Your Application
When selecting Fluorinated Ethylene Propylene (FEP) cables for industrial use, it’s essential to consider the specific environmental conditions. For instance, take into account the types of chemicals involved, as different chemicals can interact with materials in varying ways. Additionally, temperature extremes must be evaluated, since some applications may expose cables to both high and low temperatures. Furthermore, mechanical wear is another critical factor, as environments with constant movement or abrasion can lead to premature failure. By carefully considering these elements, you can ensure that the chosen FEP cables will perform optimally in their intended application. The right cable configuration can ensure optimal performance and durability, ultimately reducing maintenance costs and enhancing operational efficiency.
- Cable Types and Specifications: FEP cables come in various configurations, including shielded and unshielded options, multi-conductor layouts, and plenum-rated varieties for building installations.
- Standards and Compliance: Ensure the chosen FEP cable meets relevant industry standards like UL, CSA, and NEC, particularly if your industry requires regulatory compliance for high-performance materials.
Resources for Further Reading
- Understanding Fluoropolymer Insulation Materials
- National Electrical Code (NEC) Standards for Cable Installations
- IEEE Standards for High-Temperature Cables in Industrial Applications
Conclusion
Fluorinated Ethylene Propylene cables bring far more to the table than just oil resistance. With their ability to withstand extreme temperatures, resist harsh chemicals, and provide excellent electrical properties, FEP cables meet the rigorous demands of industrial environments. Their use reduces maintenance costs, minimizes breakdowns, and boosts operational efficiency, making them ideal for industries requiring dependable performance. As durability and efficiency remain priorities, FEP cables continue to be essential in industrial applications.
View BWC’s Oil Resistant Products